Posted on Wednesday, November 18, 2020
By:
Michele Loudenslager
Categories:
Services
|
Gas and Oil
Proper lubrication is key to the longevity of the rotating equipment. Without proper lubrication, repairs and downtime (a.k.a. money) are often required to keep your unit up and running again. Lubrication provides a low friction film for the rings, the space between the rings and cups, as well as the rings and the rod. With this helpful film, heat, leakage, and even corrosion can be combated. The major seals in a compressor, such as these piston rings and rod packing, require adequate attention and care. But sometimes oversights can happen, resulting in an irreversible outcome due to improper lubrication. Over 70% of lubrication professionals say that over lubrication is a problem at their plant.
Here are three reason why proper lubrication is so imperative to your compressors operation:
1. Too much lubrication can cause rod packing and
valve failure. Why would this happen? With too much lubrication, the packing
will lift off the rod resulting in blow-by and an undistributed amount of
pressure across the packing rings. Conversely when there is a lack of
lubrication, or worse, intermittent lube the temperature will rise due to friction
and the surfaces can take on either a
blueish or brownish hue. The temperature
can even become hot enough to cause
bearings to seize.
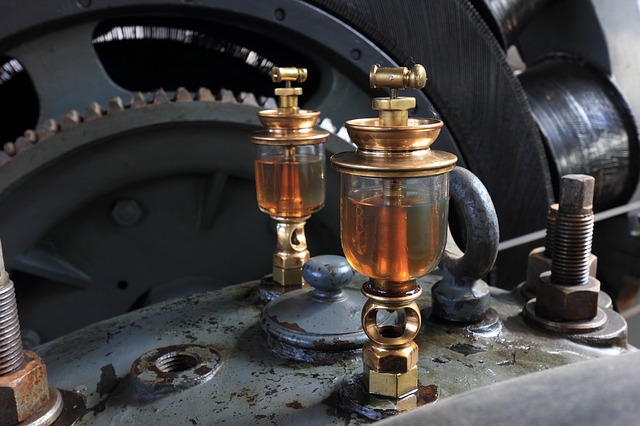
*Side
note: Did you know that grease guns can produce up to 15,000
psi? This mass amount of pressure is created when you over
grease a bearing housing causing the lip seals to rupture and allows pollutants
such as water and dirt to gain access to
the bearing housing.
2. An abundance of lubrication in the cylinder can
cause the valve sealing components to stick to the seat and guard, resulting in
increased opening and closing speeds, which will consequentially cause broken valve
components. As the oil begins to oxidize, it will form what is commonly
referred to as stiction. The word stiction is basically both static and
friction. Stiction is the
force that resists the motion
between two bodies in contact. Stiction
has a negative effect and has been known
to cause damage to the valves and subsequently
the cylinders.
3. Lubrication film, factors into the efficient
operation of a piston and the packing seals too. Irregular lubrication to these
parts will result in a loose film and
consequently build up onto the piston rod surface when instances of dry
operation occur. Similarly, with mechanical packing, over lubrication can cause
an increased amount of oxidation surrounding the parts. These formations can be
abrasive, and in some cases, it can even cause wear of the packing rings.
What can you do to avoid this?
In order to avoid the damages that
can occur with improper lubrication, Hi-Tech Compressor recommends setting up a
maintenance program that would include taking precautions with calculating the
appropriate amount and frequencies of lubrication required for each
machine/engine. Also, using feedback instruments to assist in accurate
measurements is suggested.
With these proactive steps, avoiding improper lubrication is possible. However, these actions will
help eliminate the issues seen with improper lubrication only when they are
carried out thoroughly and on a regular basis.
What kind of lubrication errors have you come across? Tell us in the comments below!
-Thank you for reading!