From its headquarters in Tullytown, Pennsylvania, USA, Hi-Tech Compressor & Pump Products (Hi-Tech) provides original equipment manufacturers (OEM) and replacement parts, reconditioning and refurbishment services, specialized products, and engineering services to companies running industrial compressors and pumps. Earlier this year Hi-Tech added to its in-house capabilities by investing in thermal spray technology, ensuring quality control and faster turnaround for its spray coating.
Gas Compression Magazine spoke with Todd Pollazzi, owner and president of Hi-Tech, about the capital investment the company made, about coatings, and about the gas compression industry Hi-Tech serves.
How does Hi-Tech’s new spray coating fit into the company’s existing capabilities/services?
Hi-Tech’s success is built upon our reputation for responsiveness, know-how, and finding new and better ways to help our customers stay up and running. Thermal spray technology is an economical way of extending equipment life and improving its performance, so it fits perfectly with what we do every day with our traditional technologies. Bringing it in-house gives us better control of quality and responsiveness. Our customers appreciate that we can now solve a wider array of problems for them.
What prompted the addition?
Hi-Tech is constantly looking for innovative techniques to help serve our customers better. We noticed that more and more customers were seeing the benefits of thermal spray technology. We had always known the potential, so it was an easy decision to improve our offering with it.
With that in mind, our spray coating addition has complemented our business services immensely. Whether it’s a piston rod that needs to be sprayed or a high-speed cylinder off a compressor, Hi-Tech is fully capable of maintaining total control throughout the parts process. In turn, this allows for a faster turnaround time.
Furthermore, with the reduction of slow-speed compressors being used in the industry and with many being replaced with gas turbines, the need to diversify our technologies was very clear. Formerly, reciprocating compressors comprised 90% of our business. The machining and pump work was less than 10%. Our metal spraying services have now increased and pump bearing housings, pump shafts, cylinders, and turbine shafts have all become a bigger part of our business.
Discuss, in as much technical detail as you can, the company’s thermal spray services – products targeted, materials/compounds offered, etc.
Hi-Tech has a wide scope of thermal spray services. The process all begins with understanding why a part is being serviced and what is the core cause or issue the customer is facing that we will correct, improve, or repair for them. Typically, the products we spray are worn, damaged, or miss-machined. Or, performance improvements are needed to prevent wear and corrosion and/or erosion using, for example, a hard coating or thermal barrier coating.
The thermal spray approach can be applied to a wide variety of materials and surfaces. Often, we can actually improve their performance because the process results in stronger resistance against typical wear and tear and other unavoidable elements.
The coatings are crucial to the spraying process because each carries its own unique attribute. The metals sprayed by our various systems range from stainless steel, Babbitt, and bronze using our twin wire arc spray, tungsten carbide using our high-velocity oxygen fuel (HVOF) system, to chromium oxide using our plasma spray. Because we have a wide range of sprays, our customers are given a variety of options, each recommended specifically for their particular needs.
An added attribute to each of our sprays is that they all provide benefits depending on what spray the customer desires.
Surface reclamation is just one of the many benefits you can receive for a worn part. By using a tungsten carbide or ceramic coating for compressor rods, the surface will be precisely reclaimed to its original state with characteristics that can look better than when purchased new.
Another benefit of the spraying process is it helps parts become more wear-resistant. Examples of sprays that provide this are tungsten carbide cobalt, tungsten carbide chrome, 400 S/S, and super alloy 97 MXC.
Corrosion resistance is a needed benefit for many parts, and Hi-Tech can achieve that with ceramic, tungsten carbide nickel (corrosion and wear), Inconel (alloy 625 equivalent), and Hastelloy (C-276 equivalent).
Thermal barrier coatings are an extremely effective way to improve the thermal properties of a product. Specifically, it is used to isolate a heat source where heat isn’t wanted and create a safe attribute of keeping the heat to a specific location. We spray a ceramic that is stable above 2000°F (1093°C) resulting in little to no machining after application.
Discuss the products and services offered by Hi-Tech today, as well as any specialized machinery in your shop to provide those services.
The products and services offered by Hi-Tech Compressor today involve all wear parts associated within a reciprocating compressor, and we manufacture parts for both OEMs and end users.
The compressor and pump parts we offer include rod packing, piston and rider rings, wiper rings, packing cases, wiper glands, valve internals, valves, valve unloaders, turbine rings, bushings and bearings, rods, pistons, crossheads, shoes, gaskets, O-rings, and polypaks. Our other products consist of engine parts, lube systems, custom made-to-order, and several specialty products.
Our reconditioning services include valves and unloaders, packing cases, oil wiper glands, piston rods, pistons, intercoolers, crossheads, connecting rods, pumps, non-destructive testing (NDT), valve cage manufacturing, case testing, in-house laser marking, actuator reconditioning, air testing, shaft straightening, cylinder re-sleeving, and clipping and boring of connecting rods in our computer numerical controls (CNCs). Because the vast majority of our work is done in-house, we can respond quickly to our customers while still controlling the quality of the finished product.
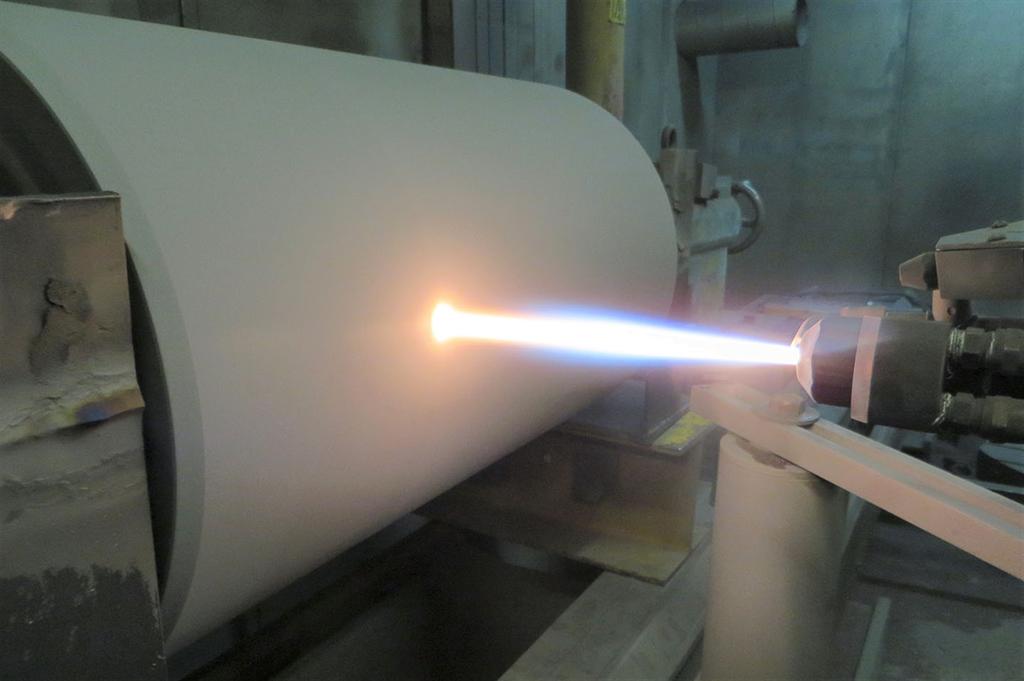
We have several specialized machines within our shop that give us a lot of flexibility to solve just about any challenge our customers can throw at us. Full-service CNC machinery enables us to manufacture critical components for in-house jobs or production runs. Our turning capacity is up to 18 in. diameter by 110 in. length (457 mm x 2794 mm). We have multiple milling machines with 20 in. long by 40 in. wide by 20 in. high (508 mm x 1016 mm x 508 mm) capacity.
Our manual machining capacity, with up to 84 in. by 40 in. by 48 in. (2134 mm x 1016 mm x 1219 mm) milling capacity and 57.75 in. by 160 in. (1467 mm x 4064 mm) long turning capacity, aids in the manufacturing of one-off parts and allows us to repair components via typical machining practices and thermal spray.
We do in-house grinding from start to finish so our metal-sprayed parts do not have to leave our facility. We have an on-site training facility and in-house NDT with class 2 certification operators.
How have customer needs and expectations changed in the past 18 years? How has Hi-Tech’s products and services changed to meet those needs?
Since we began in 1999, customers have increasingly demanded faster turnaround and a bigger bang for their buck, in addition to quality. We live in a world where technology is advancing quickly, and we have responded by adopting proven new technologies to help meet those demands. At the same time, one thing that hasn’t changed is our commitment to being easy to do business with and our responsiveness. We’ve learned the value of customer engagement, so we continue to work hard every day to communicate effectively with our customers so we can anticipate their needs and make their lives easier. Today, that includes using social media to help us maintain those relationships. Our team is always working to find new ways to help our customers save money when faced with the challenges of aging equipment.
We will continue to exploit new technologies and opportunities to help continue the innovative approach that has worked well for Hi-Tech.